- Automotive
- Sustainability
- Solutions
Slashing carbon emissions without impacting performance
Reading time: 3 minutes
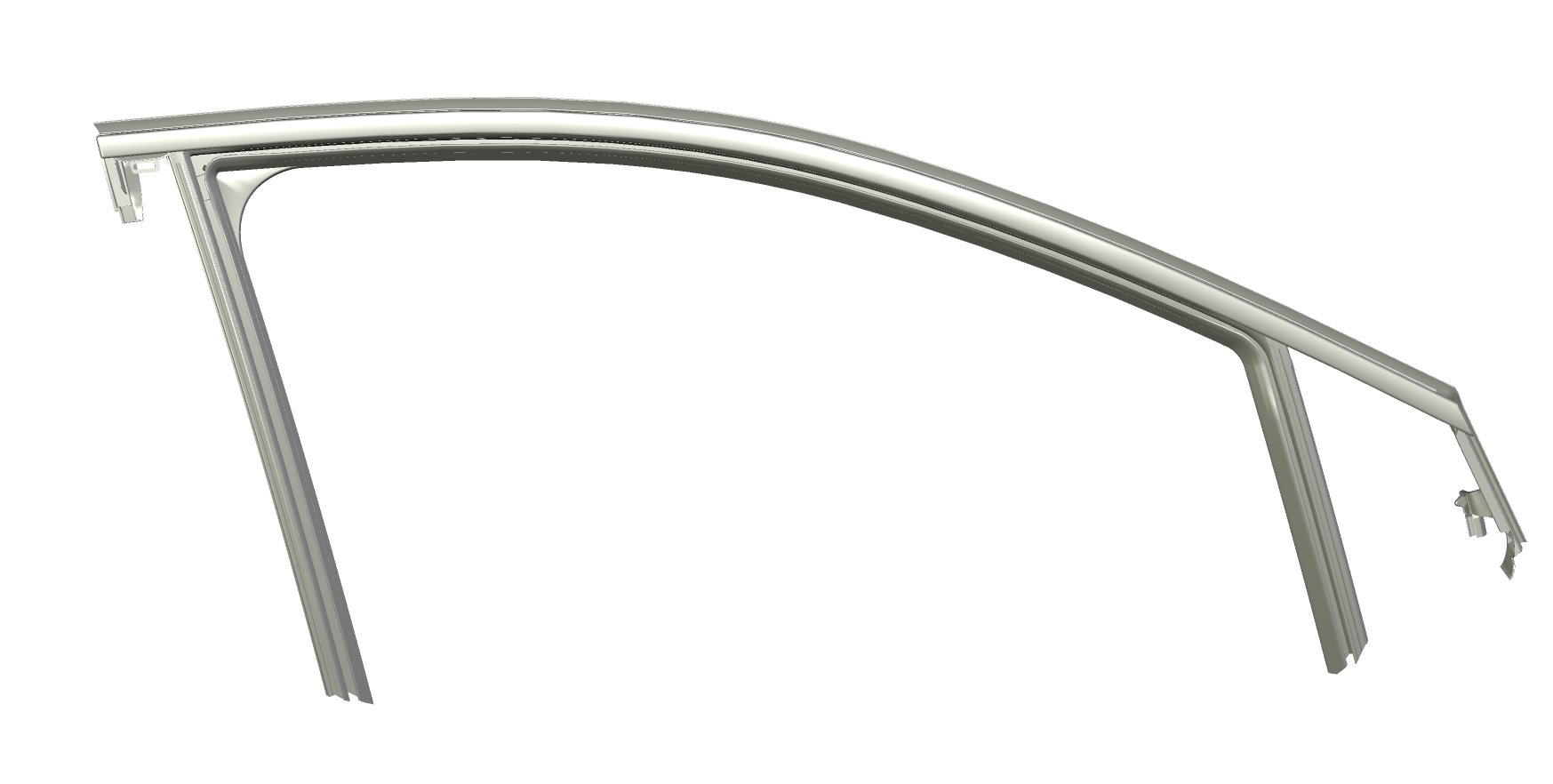
Client challenge: Design vehicle components using at least 30% sustainable plastics
With the global shift towards more sustainable solutions, car manufacturers are under increasing pressure from legislators and customers to create more ecological vehicles. In response, a major European automotive manufacturer approached Hutchinson with a challenge: create a new generation of seal for the windows of an upcoming vehicle using a material comprising at least 30% biobased, biosourced, or recycled ingredients.
The new seal had to deliver the same performance, durability, and robustness as our customer's current solution, and have no other impact on the manufacture of the vehicle's windows and doors. The only evolution would be the use of more sustainable plastic, lowering the overall lifetime emissions associated with the vehicle.
Our solution: The creation of two new materials
To engineer this solution, Hutchinson developed two new materials: revea® TPE 428, which contains 37% biobased, biosourced or recycled ingredients, and revea® TPE 426, which contains 29% biobased, biosourced or recycled ingredients. Each material worked in concert with the other, delivering the desired properties for the glass-run header, the inner waist belt, and the outer waist belt window seals.
CO2 savings were substantial, with revea® TPE 428 offering a 25% reduction in carbon emissions compared to traditional materials, and revea® TPE 426 reducing emissions by 16%, compared to existing alternatives.
Customer benefits: Same performance, added sustainability
Working with a materials expert such as Hutchinson allows OEMs to explore a multitude of new pathways to enhance their sustainability by developing alternatives to plastics, rubber, and other materials. These sustainable alternatives are engineered to deliver peak performance while making use of recycled and recyclable materials, with no impact on durability or aesthetics.
- 30% recycled material in finished product
- Up to 25% savings in CO2 emissions over lifetime of the part
With no compromise made on performance or look-and-feel, our OEM client could enhance the sustainability of its upcoming model and reduce its carbon emissions, without impacting customer satisfaction or vehicle performance.
Results: A growing portfolio of sustainable material solutions
Three years after launching this project, Hutchinson is now industrializing this solution, which will be on the road in two new vehicles by 2026. We are also exploring the possibility to launch production at our Brazilian plants to cater to customers in the Americas.
We now produce an entire range of products containing revea® materials – all of which contain at least 25% recycled or bio-based raw materials, while offering at least the same standards and performance levels as our traditional materials. The revea® range is part of Hutchinson's commitment to be carbon neutral across all scopes by 2050.
Get in touch with Hutchinson's sustainable materials specialists to discover how we can help you reduce the carbon impact of your products and make greater use of recycled and recyclable plastic.